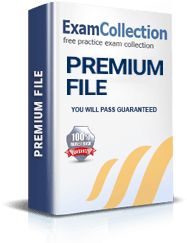
100% Real ASQ CQE Exam Questions & Answers, Accurate & Verified By IT Experts
Instant Download, Free Fast Updates, 99.6% Pass Rate
CQE Premium File: 160 Questions & Answers
Last Update: Apr 19, 2025
CQE Training Course: 347 Video Lectures
$74.99
ASQ CQE Practice Test Questions in VCE Format
File | Votes | Size | Date |
---|---|---|---|
File ASQ.passguide.CQE.v2025-03-02.by.jonathan.97q.vce |
Votes 1 |
Size 221.21 KB |
Date Mar 02, 2025 |
File ASQ.Certkiller.CQE.v2019-04-16.by.Donna.95q.vce |
Votes 3 |
Size 128.67 KB |
Date Apr 20, 2019 |
ASQ CQE Practice Test Questions, Exam Dumps
ASQ CQE Certified Quality Engineer exam dumps vce, practice test questions, study guide & video training course to study and pass quickly and easily. ASQ CQE Certified Quality Engineer exam dumps & practice test questions and answers. You need avanset vce exam simulator in order to study the ASQ CQE certification exam dumps & ASQ CQE practice test questions in vce format.
Previously in Section One A One, we talked about the evolution of quality and how it evolved over a period of time. And we also talked about the Three Quality Gurus and their philosophies. That was Section One, a one?Now, coming to section One A two, whichis continuous improvement tool here in this section,which is one A two, we will belooking at some continuous improvement tools. So what tools we are looking here? Let's look at that. So we are looking at these five continuous improvement tools in this section. The Lien. the Six Sigma theory of constraints. statistical process control and total costs. Quality management. Let's start this with Lean in the next video.
I'm coming to the first continuous improvement tool, which is lean. Nowadays, Lean and Six Sigma are very commonly used in many organizations. So these two things sort of go together: lean and Six Sigma. The only difference between these two would be that when you think of lean, you think of waste reduction. When you think of SixSigma, think of variation reduction. Leaning reduces waste. Six Sigma ensures product and process consistency. Now, coming back to lean, let's quickly look at the history of lean. The history of lean goes as far as back as 1910where the mass production was done by food and then 50s. That was the time when Japan was recovering from the war. the Toyota production system. That's another place where many of these lean tools were developed. And then in the 1990s, there was a book written that was a machine that changed the word. This was by James P. OMK. That book basically spread the word about Lean. the concept of lean in the Western world. That's the brief history of lean. When we talk of lean, lean has five philosophies. Let's quickly look at these five philosophies of lean. So the first one is value. Specify what creates value from a customer's perspective. So the emphasis in Lean is on what is valuable to the customer. Do only those things whichare providing value to customer. Anything other than that is non-value-added, or it's a waste. So that's how you define what is waste andwhat is not waste is defined by what providesvalue to the customer and what doesn't provide value. That is the first philosophy of Lean that focuses on those things that provide value to the customer. The second philosophy is the value stream. Map the value stream. In this step, we identify all of the steps in the process chain and determine which of these steps add value and which are waste. And that is the second philosophy, which is creating the value stream. The third philosophy is flow. Here, we are interested in the flow of value in the chain. So the flow makes sure that whatever you're doing is flowing, it's moving, and it's not waiting for something. Because that's another type of waste. So value should flow through the chain. And the fourth philosophy is "pull." Pull and push. If you have to distinguish between these, pulling is making something. What customers want and push for is that you make something and then try to sell it. In lean, the emphasis is on pull. Make only those things that are needed by the customer, even within the organization. Also, let's say step number two is the customer of step number one. Step number one will only produce those things that are required by step number two. When these are needed, only step number one will produce that item or that thing. So here the emphasis is on responding to the customer need rather than producing something, putting it in the inventory, and waiting for those things to sell off. So that's the fourth philosophy of leaning to produce only what is needed. The fifth philosophy is perfection, and perfection is quality. So we're aiming for perfection by constantly improving processes and making things what customers want. So all these five things make up the lean philosophy. And once again, in summary, if I have to say Lien is basically looking at waste reduction and providing value to the customer at the time when the customer wants the right quality, So this was a quick overview of Lean as a continuous improvement tool after looking at five philosophies of lean, and obviously before that, we talked about the history of lean. Now let's look at what the benefits of being lean are. So, as you would have seen when we were talking about five philosophies, the emphasis is on reducing waste. So that's the first benefit: that lean reduces waste and improves quality and customer satisfaction. Because the emphasis is on providing value to the customer, it reduces inventory. And as we said, we produce things only when they are needed. So we have a system of pull, not push. So a pull system ensures that inventories are reduced. Reduced inventories have lots of benefits. There are lots of costs that get tied up in inventory. You can save that. You don't need space to store your items,your item will not become obsolete, your itemswill not deteriorate with the time. All these are benefits of reduced inventory. And lean helps in that reducing inventory by producingwhen things are needed, it reduces cycle time. Because a value stream flow diagram tells you how much time it takes and which steps you can remove and which steps you can combine, it aids in cycle time reduction and allows you to produce things faster. That's another benefit of lean. You have flexible manufacturing because here you are looking at what the customer demands, and based on that, you need to have flexible manufacturing so that you make only those models or types of products that the customer needs. Now, rather than making lots and lots of one model, you switch to the second model and then make lots and lots of that and maintain inventory. Instead, depending on the demand, you alternate between these models. So with that, you have flexible manufacturing, which can change according to the customer's needs. And then you have a safe workplace environment because all these things will help you make your environment safe so that people can produce good-quality products and then improve employee morale. Because now employees see that whatever they are doing is valuable, they are not adding waste; they get engaged in reducing waste. So you need to engage your employees so that they also help in reducing waste. So with that, they will also have high employee morale. which will help them to make good-quality products. All of these are advantages of being lean. So that concludes our quick introduction to Lean. Now let's move on to the next continuous improvement tool, which is Six Sigma. Let's see that in the next video.
The history of Six Sigma goes back to 1924, when Walter Schuhart developed control charts. That is the foundation of Six Sigma. Then in 1987, Motorola developed the concept of Six Sigma. This concept helped this organisation to transform. And then just after one year of implementing Six Sigma, they got the Malcolm Baggage National Quality Award, which is the highest award in the US. related to quality. So that basically helped them to makea big change in the organization. So Motorola developed Six Sigma in 1987, and then after that, a lot of companies jumped into this. The most important of these is GE General Electric). They implemented Six Sigma in a big way. Then few other companies like a Light Signal,Dog Chemical, Dupont Honeywell, most of big companiesimplemented Six Sigma to improve their processes. And even today, which is, let's say, after 30 plus years, Six Sigma is still being implemented. It's not something that came and went away. For example, let's say TQM. The concept of TQM came somewhere in the 1980s, and then suddenly it vanished and nobody talked about it. Six Sigma is not one of those things. Six Sigma is even being implemented today. So this is the brief history of Six Sigma. Now coming to the philosophy of Six Sigma, Let's see that on the next slide. So here we have the Six Sigma philosophy in Lean. We talked about five key philosophies of Lean here in Six Sigma. We are talking of four key philosophies of Six Sigma. There is a lot to learn in Six Sigma. I have a number of courses on Udemy that are related to Six Sigma. White belt, yellow belt, green belt, black belt So this is a big subject in itself, so if you're interested, you can learn about that. But here we are just looking at the philosophy level, just the philosophy of Six Sigma. Let's talk about these four philosophies. Philosophy number one is to know what is important to the customer. This is something we talked about in Lean. Also, you need to see what is valuable to the customer and what gives value to the customer. In Six Sigma, we talk about what is important to the customer. and the term we use here is CTQ. And the CTQ is critical to quality. So these are the parameters that are important to the customer. The second philosophy is depicted by ctqs. So here we are looking at reducing the number of defects. And when we say reducing the number of defects, we don't mean a 1% repair rate, but a zero 1% repair rate. We are talking about 3.4 defects per million opportunities. It's a very small level of defect. So that's what we focus on. So Six Sigma focuses on 3.4 defects per million opportunities, which is DPMO. Third philosophy: centre around the target or around the mean. So what we attempted to do is, let's say we were making a 100-mm shaft that has a tolerance of plus or minus five, so this shaft could be 100 mm or anything between 95 and 105 mm. But here in Six Sigma, what we attempt to do is target around the mean target of 100, rather than just being within 95 and 105. That's another philosophy that means we need to be focused around the center. And then we are looking at the reduction in variation. And when I say the same example of shaft, my shaft could be 95 to 105 mm. So here we are looking at reducing variations. So, rather than one shaft being 95 and the second shaft being 10, 5, even though these are within tolerance, within the acceptable limit, our attempt would be to reduce that variation, making it something closer to 100 rather than plus or minus five. Let's see if we can make it plus or minus one millimeter. So that's something that we need to have in Six Sigma. So this was philosophy number four, which is reduced variation. So earlier, we talked about the philosophy of Six Sigma. There were four philosophies related to Six Sigma. Now we are talking about Six Sigma benefits. And even before I talk about these benefits, let me quickly tell you about two approaches to Six Sigma. When you do a Six Sigma project, you do two approaches, DMAC and DMAD V. So if you have an existing process and you want to improve that process, in that case, you use the DMAC approach. Let me write it here. So D Max is D for define, M for measure, A for analyse, I for improve, and C for control. So this is a cycle of "define, measure, analyze, improve, and control." This is for the current process. And then if you are developing a new process that will make sure that your process is a Six Sigma process, in that case, you use the Mad V approach. The Mad V. defines, measures, analyses, designs, and verifies. So these are the two approaches in Six Sigma. Now, having talked about these two approaches, let's quickly look at the benefits of Six Sigma. The first benefit of Six Sigma is that this generates sustained success. Six Sigma is done project by project. So you do one project, and you save some money. Because of that, you make some improvements. And those improvements help organisations save some money. That is not a one time event. So whatever money you save, that's saved year after year, time after time. So the success that this process, which is Six Sigma, generates is sustained success. It's a recurring benefit. It's not a one-time benefit. The second thing here is that SixSigma projects are tied to organisational strategy. So it's not like you can just pick one project and start working on it. The projects are systematically selected and tied to what the organisation wants to do over a period of time. What is the organization's strategy? So you select a project which basically helpin making profit or which are customer focusedso those sort of the projects you pick. The third point here is that project outcomes are tied to financial reporting systems. So each Six Sigma project will help in saving some money. Whatever improvement you make, that can be translated in terms of money. And that's the language management uses to understand whether you have reduced the number of defects or whether you have made some processes faster. Anything can be translated in terms of financial gains. So Six Sigma's outcome is tied to financial gain. These gains are even reviewed by financial analysts to confirm that, yes, this is the real gain. So this was the process before the Six Sigma project, and this was the process after the Six Sigma project. And this is what it saves per year. So project outcomes are tied to the financial system. In Six Sigma, you have a number of belts. white belt, yellow belt, green belt, black belt, and master black belt. So this is the hierarchy of belts. Any person who is new to Six Sigma starts with a white belt. White belt gives you a very high-level overview of Six Sigma. Then you go to the Yellow Belt. So once you have earned your yellow belt, then your yellow belts are able to help. In Six Sigma projects, they are basically participants or the people who are working on that Six Sigma project. So yellow belts are basically the participants in the project. Then you have a green belt. If you have completed green belt, you will most likely be able to lead a Six Sigma project of lower complexity. With the black belt, you can lead a complex Six Sigma project. A master black belt is somebody who teaches the Six Sigma philosophy. Or he is the master of Six Sigma in the organization. And then in Six Sigma, we have a reward and recognition system. Since every project is tied to financial gains, there could be a reward associated with successful completion of the project. So this will all depend on the organization. So this was basically a quick overview of Six Sigma. We talked about a brief history of Six Sigma. We talked about Six Sigma philosophy. We even talked about two approaches to Six Sigma. For an existing process, we used a DMAC approach. And for a new process, we use the MadV process, defined as measure, analyze, design, and verify. And we talked about Six Sigma's benefits. So with this, we complete the second continuous improvement tool in this section, which is Six Sigma.
In continuous improvement tools. So far, we have talked about Lean and Six Sigma. If you look at CQE, which is thecertified quality engineer body of knowledge, there arefive continuous room and tools listed in that. The third tool listed in the body of knowledge is the Theory of Constraints. Eliyahu Goldrat introduced the theory of constraints in his book The Goal. If you look at this book, The Goal, it is written in the form of a novel or a story. How a production manager improves the process in a company that is about to go bankrupt and close how this person, the production manager, goes step by step to identify where the improvement is needed. The theory of constraints proposes that you identify constraints, or things that limit your ability to achieve the goal. So, let's say you're manufacturing some items, and there's a series of events that happen. There are a number of steps being done in that.That particular step is basically a constant. So you need to identify that constant and work on it. On the next slide, I will explain that with the help of an example there. And this is a repeated process. So you identify a constraint, you overcome that, then there will be another constraint, you overcome that, and so on. So that's how you improve your production rate. So this is about the theory of constraints in very plain, simple language in the summary. So consistency is the weakest link in the change. So you identify the weakest link and then attend to that. That's how you can improve your process. So earlier, too, when we talked about Lean and Six Sigma, we talked about projects and about improvement. And in Six Sigma, we talked about selecting projects based on an organization's strategy. But that's where the theory of constraints helps in identifying what needs to be improved. So you improve only those things that are in need of improvement. Let's take a simple example to understand how things work in chains. Let's say I'm creating this course. So, for creating this course, the first step would be to do some research and make slides. Let me put it here. So step number one would be to make slides. So that's my step number one, slides. Once I have done that part, then my next process would be to record this, which I'm doing right now, recording these lectures. And the next step would be editing these, adding an introduction, an intro, a closing, and removing anything that is duplicated or mistaken. So that is editing. So this is how I go about my process of making these lectures. Anything in the industry will work like this. There will be steps one, two, and three. You take a rough shaft, you cut that, you do the number of things you do, and then you do welding. Let's take another simple example, where you do three steps in an industrial environment. So let's say this is step number one, then it goes to step number two. Then this piece moves to step number three. Each of these three machines, which are doing these three steps, has a different capacity. Let's say this particular one, which is machine number one, can make 60 pieces per hour. Machine number two can make 30 pieces per hour, and machine number three will make 60 pieces per hour. If this is the capacity of these three machines, and if things are moving in a chain, what do you think would be the overall capacity of this process? If you have guessed 30 pieces per hour, you are right, because this is the constant here. Process number two is the constant And because of this, your output would beyour output would be 30 pieces per hour. And this is because of constant process number two. Now, if you want to improve this process and make it produce more, which process do you think you should be working on? Let's say if we decide that's okay, we can improve process number one. So instead of 60 pieces per hour, let's improve this process and make it 100 pieces per hour. We identified the problem, we did some projecting on it, and we found a way to increase the capacity of machine number one from 60 to 100. Would that make any difference? Yes, you guessed it right. No, it won't make any difference. So instead of 60 pieces, this will produce 100 pieces, but the next process just needs 30 pieces. The rest will be waiting for machine number two to do the process. Your output would still be 30 pieces per hour. But instead of that, if you work on that constraint, our constant is number two. If you work on this constraint and instead of 30 pieces per hour, you could make it, let's say, 40 pieces per hour, then what? You would see that your total output of the production increases from 30 to 40 because you remove this constant, or you are tempted to do so, and you improve the capacity of that. Now, instead of 40, let's say you do another project and make it at, let's say, 200 pieces per hour. So by increasing the capacity to 200 pieces per hour, now you would see that the overall production has gone from 40 to 60 pieces per hour. Now what has happened is that machine number one has become a constraint. So now the constraint has shifted. So once you have attended to one constraint, the constraint will move to something else. So this is all about the theory of constraint in a very plain and simple language. Let's look at this slide here; it helps identify what to improve. We talked about how the current constraint should always be the top priority to make improvements. So if you have to make any improvement, you should be looking at whatever the current constant is. So initially, number two was the constant. So we were working on improving that process only, and improving a non-constant process will not improve the overall throughput. So instead of improving on process 1, if initially we improved process 1 and made it 100, that didn't help. So it's a non-constant process; if you improve that, that doesn't help. And what are the examples of the constant? An example of the constant could be a physical constraint. Let's say machine capacity. There could be a policy constraint requiring that a specific unit produce these many tonnes per hour, per day. There could be some kind of policy or paradigm. As if you believe this is a constant that may or may not be constant. and the constant could be the marketplace. So there could be a number of constants. Look at that, identify that, and work to remove that constant. So this is about the theory of constraint. On the next slide, we will look at the steps for removing constraints. So let's look at that as well. So here we have five steps in the theory of constraint. The first step is to identify the current constraint. And that is what we understood. If you identify the current constraint, then you can work on that. Then you exploit or make improvements using existing resources. So whatever way you can improve that process, you do that. The third step is subordinate. Subordination entails making certain that all activities support the constant. What that means is, let's say machine number two initially was constant because it was producing 30 items; make sure that everything basically works towards improving that constraint. So if, let's say, machine one was producing more, if somehow we could use a part of that machine to make more of process number two, that could be done. So whatever resources you have, make sure that those resources are focused towards reducing that constant or acting on that constant. The fourth step is elevated. If this constant still exists, then take further action. Whatever management involvement is required, you need to have another machine in step number two. Have that. The last step is to repeat. Because constant will move. So if you remove one constant, then you might have another constant. So you need to repeat this whole process of identifying, exploiting, subordinating, elevating, and repeating. So this was all about the theory of constants. Click. And it's.
The fourth continuous improvement tool, which I want to discuss in this section, is statistical process control. So far, we have talked about lean-six-sigma and the theory of constraints. And this one is the next one, which is statistical process control. Here in this section, I will just give you a very high-level overview of the area. This particular improvement tool, which is SPC Statistical process control has been covered in quite a lotof details in section six F of this course. So if you look at the body of knowledge for CQE in 6F, you will see that there is a section on statistical process control. So we will talk about that in detail there. But right now, let's just have a quick look at what SPC, or statistical process control, is. When you think of SPC, you think of control charts. Even six sigma is also based on statistical processcontrol because initially prior to six sigma there usedto be control charts where the process used tobe controlled in plus minus three sigma limits. Six Sigma was an extension of that, taking the control charts to the next level. So this was basically a quality control tool to control the processes to make sure that they are acting within the next limit (upper control limit, lower control limit). And if there is any change in the process, an alert would be given in the form of the control chart. So control chart points will show something wrong, and then you can act on that. So this was a tool for quality control. Now in this, there are two aspects that we need to consider, namely the common cause and the special cause. Anything has variations. So whatever you see, there's a variation in that.You really cannot make all 100 pieces the same size and length. So, if you make a 100 mm rod, some will be slightly larger and some will be slightly smaller. There is variation in everything. But then there are two causes of variation. One is the common cause, and the second is the special cause. Of course, we will be talking about that in detail once we go to Section 6 F. But keep in mind that the common cause is something you can't really control, which is inherent variation. On the other hand, when we talk of a special cause, this is something that is assignable—you can assign that particular variation to some particular thing and say that this particular change happened because of this particular thing. So if you attend to that, you can remove that particular cause, and you can bring your process back under control. So that is a special cause. And as I earlier told you, control charts are used for statistical process control. Here a dimension is measured and put on a control chart. If a point goes above or below the upper control limit or lower control limit, then we get an alert that something has changed and should take action. So this was a quick, brief introduction to statistical process control. So with that, let's finish statistical process control here and move on to the next improvement tool, which is total quality management. Let's see that in the next video.
Go to testing centre with ease on our mind when you use ASQ CQE vce exam dumps, practice test questions and answers. ASQ CQE Certified Quality Engineer certification practice test questions and answers, study guide, exam dumps and video training course in vce format to help you study with ease. Prepare with confidence and study using ASQ CQE exam dumps & practice test questions and answers vce from ExamCollection.
Purchase Individually
ASQ CQE Video Course
Site Search:
SPECIAL OFFER: GET 10% OFF
Pass your Exam with ExamCollection's PREMIUM files!
SPECIAL OFFER: GET 10% OFF
Use Discount Code:
MIN10OFF
A confirmation link was sent to your e-mail.
Please check your mailbox for a message from support@examcollection.com and follow the directions.
Download Free Demo of VCE Exam Simulator
Experience Avanset VCE Exam Simulator for yourself.
Simply submit your e-mail address below to get started with our interactive software demo of your free trial.
Add Comment
Feel Free to Post Your Comments About EamCollection VCE Files which Include ASQ CQE Exam Dumps, Practice Test Questions & Answers.