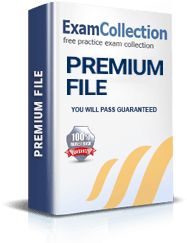
100% Real Six Sigma LSSBB Exam Questions & Answers, Accurate & Verified By IT Experts
Instant Download, Free Fast Updates, 99.6% Pass Rate
LSSBB Premium File: 300 Questions & Answers
Last Update: Jun 15, 2025
LSSBB Training Course: 45 Video Lectures
$74.99
Six Sigma LSSBB Practice Test Questions in VCE Format
File | Votes | Size | Date |
---|---|---|---|
File Six Sigma.questionspaper.LSSBB.v2025-05-18.by.ruby.165q.vce |
Votes 1 |
Size 1.59 MB |
Date May 18, 2025 |
File Six Sigma.Examskey.LSSBB.v2019-03-11.by.Ronnie.182q.vce |
Votes 3 |
Size 1.66 MB |
Date Mar 12, 2019 |
Six Sigma LSSBB Practice Test Questions, Exam Dumps
Six Sigma LSSBB (Lean Six Sigma Black Belt) exam dumps vce, practice test questions, study guide & video training course to study and pass quickly and easily. Six Sigma LSSBB Lean Six Sigma Black Belt exam dumps & practice test questions and answers. You need avanset vce exam simulator in order to study the Six Sigma LSSBB certification exam dumps & Six Sigma LSSBB practice test questions in vce format.
Go to testing centre with ease on our mind when you use Six Sigma LSSBB vce exam dumps, practice test questions and answers. Six Sigma LSSBB Lean Six Sigma Black Belt certification practice test questions and answers, study guide, exam dumps and video training course in vce format to help you study with ease. Prepare with confidence and study using Six Sigma LSSBB exam dumps & practice test questions and answers vce from ExamCollection.
Purchase Individually
Six Sigma LSSBB Video Course
Site Search:
SPECIAL OFFER: GET 10% OFF
Pass your Exam with ExamCollection's PREMIUM files!
SPECIAL OFFER: GET 10% OFF
Use Discount Code:
MIN10OFF
A confirmation link was sent to your e-mail.
Please check your mailbox for a message from support@examcollection.com and follow the directions.
Download Free Demo of VCE Exam Simulator
Experience Avanset VCE Exam Simulator for yourself.
Simply submit your e-mail address below to get started with our interactive software demo of your free trial.
Add Comment
Feel Free to Post Your Comments About EamCollection VCE Files which Include Six Sigma LSSBB Exam Dumps, Practice Test Questions & Answers.