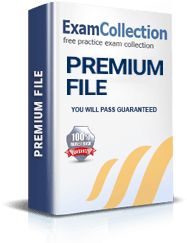
100% Real Six Sigma LSSYB Exam Questions & Answers, Accurate & Verified By IT Experts
Instant Download, Free Fast Updates, 99.6% Pass Rate
LSSYB Premium File: 150 Questions & Answers
Last Update: Jun 07, 2025
LSSYB Training Course: 84 Video Lectures
LSSYB PDF Study Guide: 382 Pages
$79.99
Six Sigma LSSYB Practice Test Questions in VCE Format
File | Votes | Size | Date |
---|---|---|---|
File Six Sigma.testking.LSSYB.v2025-05-31.by.holly.187q.vce |
Votes 1 |
Size 510.86 KB |
Date May 31, 2025 |
File Six Sigma.Actualtests.LSSYB.v2019-05-12.by.Massimo.190q.vce |
Votes 3 |
Size 561.58 KB |
Date May 12, 2019 |
Six Sigma LSSYB Practice Test Questions, Exam Dumps
Six Sigma LSSYB (Lean Six Sigma Yellow Belt) exam dumps vce, practice test questions, study guide & video training course to study and pass quickly and easily. Six Sigma LSSYB Lean Six Sigma Yellow Belt exam dumps & practice test questions and answers. You need avanset vce exam simulator in order to study the Six Sigma LSSYB certification exam dumps & Six Sigma LSSYB practice test questions in vce format.
Go to testing centre with ease on our mind when you use Six Sigma LSSYB vce exam dumps, practice test questions and answers. Six Sigma LSSYB Lean Six Sigma Yellow Belt certification practice test questions and answers, study guide, exam dumps and video training course in vce format to help you study with ease. Prepare with confidence and study using Six Sigma LSSYB exam dumps & practice test questions and answers vce from ExamCollection.
Purchase Individually
Six Sigma LSSYB Video Course
Site Search:
SPECIAL OFFER: GET 10% OFF
Pass your Exam with ExamCollection's PREMIUM files!
SPECIAL OFFER: GET 10% OFF
Use Discount Code:
MIN10OFF
A confirmation link was sent to your e-mail.
Please check your mailbox for a message from support@examcollection.com and follow the directions.
Download Free Demo of VCE Exam Simulator
Experience Avanset VCE Exam Simulator for yourself.
Simply submit your e-mail address below to get started with our interactive software demo of your free trial.
i am very happy that i have known how to open lssyb vce file in the vce player. i will use the vce file for lssyb exam in my preparation for the main exam. i hope it will aid me towards success in the lssyb cert exam.
guys, braindumps for lssyb exam are all you need to clear the cert exam successfully. i passed the test last month using them.
wow! what an excellent performance! lssyb practice exam questions and answers are nice. they have helped me score 83 percent in the lssyb cert exam. i recommend.
lssyb cert exam really stressed me before i came across lssyb premium files. they were very informative regarding the concepts tested in the lssyb exam. i recommend them to anyone who is waiting for lssyb exam and want to attain the passing score.
after all the struggle, i have managed to find reliable lssyb prep materials and finally hit the passing score. thanks to everyone who has contributed towards my success.
practice test for lssyb exam has helped me greatly. it has enabled me to understand concepts which are often tested in the test. i wish the exam was scheduled to be done today or tomorrow. i feel am fully prepared to take the exam.
guys, lssyb premium file is exactly what you require to achieve academic excellence in the real exam. it comprises questions which are alike with those in the real test. i used it to revise for the test and i am joyful for succeeding in the test.
lssyb cert exam was difficult though i was able to excel. thank you guys for offering vce files for lssyb which are reliable. the really helped me to avoid failure in the test.
i am grateful for lssyb dumps. they contributed a lot towards my success in the lssyb cert exam.
@anastacia, i have experience on lssyb exam, i sat for this exam last month and passed. i think you need to study various learning materials relevant to this exam and get various practice questions from the website of examcollection for testing your readiness for the exam.
how is lean six sigma yellow belt cert exam? those who have experience on lssyb cert exam what does someone need so as to pass this test? i am preparing for the test, hope i will perform well.
Add Comment
Feel Free to Post Your Comments About EamCollection VCE Files which Include Six Sigma LSSYB Exam Dumps, Practice Test Questions & Answers.